Burnt Clay Hollow Blocks: a modern material for low- carbon buildings
- theA&Pnews
- May 6
- 3 min read
The article authored by Dr Sameer Maithel dedicates itself to the low-carbon buildings. In this attempt of sustainable construction, burnt clay hollow blocks have emerged as an excellent walling material. This is also accompanied by reducing both embodied and operational carbon in buildings and faster and enhanced quality of construction. On this basis, it could be one of the ideal materials for constructing new housing.

Introduction
India is expected to construct around 100 million new homes during next 10 years (Swaminathan 2024). During the life cycle of a building, the largest carbon emissions are:
(a) cradle to gate embodied carbon emissions, occurring during the product stage, that is, in mining, transportation of raw material and manufacturing of construction materials like steel, cement, brick, glass, and so on, (b) operational carbon emissions, occurring during the operation (heating, cooling, lighting, and so on) of the building. It is critically important that the new housing being constructed has low embodied and low operational carbon emissions.
A significant percentage of the new housing construction is expected to be RCC frame structure with masonry infill walls made from bricks. In such constructions, the walls can contribute up to 25% of the cradle to gate embodied carbon emissions (Chetia, Mital, Phogat, et al. 2024). The thermal properties of bricks impact the heat transfer across the building envelope and the energy used for cooling and heating of the building. One of the ways to reduce life cycle carbon emissions of new housing is to choose bricks that have low embodied carbon, this also helps in reducing operational carbon emissions. Burnt clay hollow block is one such promising material available in the Indian market.

Burnt Clay Hollow Blocks
In South Asia, burnt clay bricks have been widely used since the Indus Valley civilization. Even today, burnt clay solid bricks have the largest market share among masonry materials in India. The popularity of burnt clay bricks
is attributed to good strength, durability, dimensional stability, resistance to fire, breathability, amongst others (Bender and Handle 1982). Burnt clay bricks are also free from toxic materials, easy to reuse and recycle.
The Bureau of Indian Standards (BIS) defines a burnt clay hollow block as a block in which holes pass through the block exceed 25% of its volume and thus are not small (IS 2248:1992). The hollows may be at right angle or parallel to the bearing surface. Burnt clay hollow blocks have been widely used for decades in Europe, South America, and the Middle East. In India, burnt clay hollow blocks were manufactured in small quantities in roofing clay tile factories in Kerala for decades, it is only after the starting of the operation of Wienerberger India factory located near Bangalore in 2009, their availability increased in South India, and being used in large residential building projects.
In recent years, some of the brick manufacturers located in North India, like Prayag Clay Products Limited (PCPL), Varanasi and Jindal Ceramica, Jhajjar have modernized their brick- manufacturing plants and started manufacturing hollow blocks, thus improving their availability nationally.
Types and specifications of hollow blocks
Today, several types of burnt clay hollow blocks are available in the Indian market. They can be broadly categorized as:

a) horizontally perforated clay blocks (Image 1), which have compressive strength ≥ 3.5 N/mm2, and are suitable
for non-load bearing construction and b) vertically perforated clay blocks (Image 2), whichhave compressive strength ≥ 7 N/mm2, and are suitable for load-bearing construction.
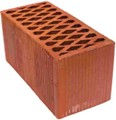
The density and water absorption of these blocks typically range from 700–950 kg/m3 and 10–20%, respectively. The blocks are available in several sizes (Table 1). Some innovative products like interlocking blocks (Image 3) which due to its interlocking feature reduces the amount of mortar requirement and insulation filled hollow blocks (Image 4) which provide higher thermal insulation are also available. Some of the hollow blocks also carry
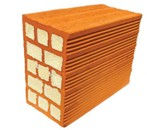
GRIHA certification. While the conventional cement– sand mortar can be used for laying these blocks, dry mortar or super glue, which does not require any curing is also available. Training programmes to train masons for using these blocks are also being offered by the manufacturers.
Table 1: Size and application of some types of hollow blocks available in the Indian market
Product | Length × width × height (mm) | Application |
Horizontally cored clay block | 400 × 200 × 200 | Non-load- bearing wall |
400 × 150 × 200 | ||
400 × 100 × 200 | ||
Vertically cored clay block | 400 × 200 × 200 | Load-bearing wall |
400 × 150 × 200 | ||
280 × 205 × 130 | ||
280 × 135 × 130 | ||
280 × 70 × 130 |

Reduction in Operational Carbon
The U-value (thermal transmittance) of the walls made from burnt clay hollow blocks is significantly lower compared to the wall made from solid burnt bricks or concrete walls. The U-value of walls constructed using burnt clay hollow blocks with wall thickness, ranging from 100 mm to 200 mm, varies from 1.0 to 1.7 W/m2K (Wienerbergern.d.). A report based on lab testing of hollow blocks at CEPT, University at Ahmedabad, reports U-value ranging from 1.69 to 1.83 W/m2K for walls made from 200 mm thick hollow block and 0.75 W/m2K for a composite wall of 200 mm thick hollow block with XPS insulation (Rawal, Shukla, Shah, et al. 2022). The same study reports the U-value of a 250-mm thick wall made from solid burnt clay brick as 2.41 W/m2K and that of a 100-mm thick RCC wall as 3.59 W/m2K. The lower U-value of walls made from burnt clay hollow blocks helps in improved indoor thermal comfort and in reducing operational energy required for air conditioning.
Reductions in Embodied Carbon
The cradle to gate embodied carbon analysis depends heavily on the technology for manufacturing bricks and fuel used. The results of a study on cradle to gate embodied carbon emissions of solid and hollow products manufactured at a
plant located in Varanasi (Maithel, 2023) show huge reductions in carbon emissions:
A 31% reduction in cradle to gate embodied carbon emissions for a type of
vertically cored hollow block (137.3 kgCO2/m3), compared to burnt clay solid brick (198.9 kgCO2/m3).
A 55% reduction in carbon emissions (kgCO2/m2 of wall) for a 150 mm thick wall made of hollow block compared to a 230 mm thick wall of solid brick.
Material Savings and Faster Construction
In addition to the reductions in carbon emissions, the hollow blocks also result in huge material savings. For the study quoted above for embodied carbon, there is a saving of 58% in soil requirement for manufacturing, around 60% savings in cement and sand consumption in mortar (per m2 of wall area) as well as a reduction in the quantity of steel and concrete due to lower weight of the hollow blocks (Maithel 2023). Owing to large format size, construction is faster with hollow blocks.
Conclusion
Burnt clay hollow blocks are an excellent walling material which helps in reducing both embodied and operational carbon in buildings as well as faster and enhanced quality of construction. They can be one of the ideal materials for constructing
new housing (Figures 5 and 6). Government agencies like the BMTPC and green building rating agencies like GRIHA can play an important role in increasing the demand for the burnt clay hollow blocks. On the supply side, if the government can initiate actions to indigenize modern technology for extrusion, drying and firing and facilitate finance to brick industries, it will help in modernizing the brick industry and in rapidly increasing the supply and bringing down the cost of burnt clay hollow blocks.
Article shared by Mr. Satya Pal Jindal Partner at Jindal Ceramica |Clay Building Materials |Thermobrick (Porotherm) | Green building products
(through LinkedIn connection)
References
Swaminathan, H. 2024. India will need to build 100 million homes this decade amid rising household incomes. The Economic Times, 13 June
Chetia, S., N. Mital, S. K. Phogat,
P. Bhanware, M. Jain, S. Maithel, and H. Patel H. 2024. Whole-life carbon analysis of residential buildings in India: three case studies from Bengaluru. Greentech Knowledge Solutions, New Delhi
Bender, W. and F. Handle. 1982. Brick and Tile Making,
Bauverlag, Wiesbaden, Berlin, Germany
IS 2248: 1992 Indian Standard: glossary of terms relating to clay products for buildings, Bureau of Indian Standards, New Delhi
Maithel, S. 2023. Innovative Burnt Clay Brick Construction Technology for Low-Carbon
and Resource Efficient Housing in the Indo–Gangetic Plains.
Comfort at the Extremes (CATE 2023), 13–15 December. CEPT
University, Ahmedabad, India
Rawal, R., Y. Shukla, A. Shah, G. Gowri, B. Pathak, Sankalpa,
M. Narendran, N. Bhesaniya, and S. Das. 2022. Thermal performance of walling material and wall technology, Part-2. Details available at
Wienerberger India Private Limited. Details available at
<https://www.wienerberger. in/products/wall/porotherm- smart-bricks.html>
Comments